Offre de thèse
Interface et Impression 3D vers l'impression 4D : Impression 3D réactive à l'interface de multimatériaux thermoplastiques
Date limite de candidature
11-05-2024
Date de début de contrat
01-10-2024
Directeur de thèse
NOUVEL Cécile
Encadrement
Directeur de thèse : NOUVEL Cécile - LRGP - Professeure Université de Lorraine - cecile.nouvel@univ-lorraine.fr Co-directrice de thèse : HOPPE Sandrine - LRGP - Chargée de Recherche CNRS HDR - sandrine.hoppe@univ-lorraine.fr Le doctorant bénéficiera de la stratégie d'accueil et d'accompagnement du LRGP : accueil administratif, accueil par une journée dédiée organisée le bureau des jeunes chercheurs, une visite et formation en sécurité, participation à des séminaires de conférences scientifiques et des assemblées scientifiques A cela s'ajoutent de très bonnes conditions matérielles (espace bureau dédié, ordinateur récent à disposition, équipement du laboratoire adéquat…) et de suivi (incitation à participer à des formations et des journées scientifiques en plus de celles proposées par l'école doctorale, réunions mensuelles et points de suivi réguliers, Nous inciterons de plus le doctorant à présenter ses travaux dans un congrès international et au moins une fois dans un congrès national, ainsi qu'à participer à des journées scientifiques de la SFGP (société française de génie des procédés) ou du groupe Français des polymères (GFP).
Type de contrat
école doctorale
équipe
Axe 5 - GENIE DES PRODUITScontexte
Amélioration des procédés de fabrication d'objets polymères par impression 3D, tout en conservant le caractère recyclable des objets obtenus.spécialité
Génie des Procédés, des Produits et des Moléculeslaboratoire
LRGP - Laboratoire Réactions et Génie des Procédés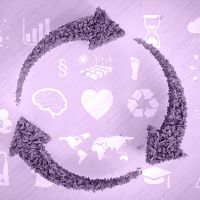
Mots clés
Fabrication additive, Impression 4D, Dépôt de Fil Fondu, Extrusion, Multimatériaux, Interface
Détail de l'offre
Les méthodes de fabrication additive possèdent un grand potentiel de développement pour les prochaines décennies à condition qu'un certain nombre de verrous scientifiques soient levés [1-3]. Actuellement parmi les techniques de fabrication additive, l'impression par dépôt de fil fondu (Fused Deposition Modeling-FDM) est la technique la plus abordable ainsi que la plus facile à mettre en œuvre en milieu non environné. Son procédé dérivé, par extrusion directe de granulés (Fused Granulate Fabrication-FGF), permet notamment d'envisager des solutions de recyclage des matériaux polymères en circuit court [4]. L'un des enjeux majeurs des méthodes de fabrication additive se situe dans la réalisation d'objets multimatériaux [2, 5] qu'il s'agisse de combinaison polymère/métal (ex : incorporation de capteurs électroniques dans un objet polymère) et/ou polymère thermoplastique (dur)/polymère thermoplastique élastomère (souple). Dans les objets réalisés jusqu'à présent, un problème de cohésion découle de la mauvaise adhérence des matériaux de nature différente à l'interface entre les couches, ce qui limite les propriétés mécaniques des objets obtenus [5]. Pour résoudre ce problème, ce projet visera à développer un nouveau procédé innovant combinant impression 3D de type FDM et réaction chimique. Bénéficiant des expertises complémentaires des personnels de l'ERPI et du LRGP, en impression de type FDM [3-4], en extrusion réactive [6], en chimie des polymères aux interfaces [7-8] et en mécanique des matériaux [3], diverses solutions seront progressivement envisagées soit la co-extrusion de mélanges thermoplastiques incorporant des polymères fonctionnalisés, soit le co-dépôt d'un filament polymère fondu et d'un mélange de type « colle » réactive. Outre l'optimisation de ce procédé, un des enjeux sera de synthétiser ces polymères fonctionnalisés et formuler cette « colle » pour qu'elle réponde au cahier des charges (en matière de réactivité, propriétés thermiques et rhéologiques permettant son dépôt, adaptation et évolution en fonction de l'environnement, recyclabilité finale de l'objet, …). Différents systèmes réactifs sont envisagés mais l'objectif sera de viser un caractère réversible de la réaction sous l'effet d'un stimulus (température ou modification du potentiel réducteur du milieu) selon le type de réaction, permettra de conférer in fine aux pièces finales un effet 4D (i. e. des fonctionnalités évolutives au cours du temps sous l'influence d'un stimulus : propriétés autoréparantes ou déformation potentielle) [8]. Ainsi, cela ouvrira la voie vers des objets multipolymères/matériaux imprimées potentiellement évolutifs (effet 4D) ouvrant la voie vers de nombreux domaines d'applications (capteur embarqué, objet aux propriétés mécaniques adaptables voir évolutives, (endo)prothèse mobile ou évolutive…).
Keywords
Additive manufacturing, 4D Printing, Fused Filament Fabrication, Extrusion, multimaterials, Interface
Subject details
Additive manufacturing methods have a great development potential in the coming decades provided that a certain number of scientific bottlenecks are orvercome [1-3]. Currently, among additive manufacturing techniques, Fused Deposition Modeling (FDM) is the most affordable and easiest to implement in a non-customized environment. Fused Granulate Fabrication (FGF), a process derived from direct granule extrusion, offers the potential for short-circuit recycling of polymer materials [4]. One of the major challenges of additive manufacturing methods lies in the production of multi-material objects [2, 5], whether polymer/metal combinations (e.g. incorporating electronic sensors into a polymer object) and/or thermoplastic polymer(hard)/elastomeric thermoplastic polymer (flexible). In the objects produced to date, a cohesion problem arises from the poor adhesion of materials of different natures at the interface between layers, which limits the mechanical properties of the final objects [5]. To solve this problem, this project aims to develop a new, innovative process combining FDM-type 3D printing and chemical reaction. Drawing on the complementary expertise of ERPI and LRGP staff in FDM-type printing [3-4], reactive extrusion [6], polymer chemistry at interfaces [7-8] and the mechanics of materials [3], various solutions will be progressively considered: either co-extrusion of thermoplastic blends incorporating functionalized polymers, or co-deposition of a molten polymer filament and a reactive 'glue'-type mixture. Besides the optimization of this process, one of the challenges will be to synthesize these functionalized polymers and formulate this 'glue' so that it meets the required specifications (in terms of reactivity, thermal and rheological properties enabling it to be deposited, sensitivity to the environment, final recyclability of the object, etc.). Various reactive systems are envisaged, but the aim will be to ensure that the reaction is reversible under the effect of a stimulus (temperature or change in the reducing potential of the medium), depending on the type of reaction, so as to give the final parts a 4D effect (i.e. evolutionary functionalities over time in response to the stimulus, self-healing properties or potential deformation) [8]. This will pave the way for potentially evolving multi-polymer/printed material objects (4D effect), opening the way to a wide range of applications (embedded sensor, object with adaptable or evolving mechanical properties, mobile or evolving (endo)prosthesis, etc.).
Profil du candidat
Le ou la candidat(e) devra posséder un diplôme d'ingénieur ou de Master 2 recherche, en science des matériaux, en génie des procédés, en plasturgie, ou encore en chimie des polymères. Des compétences dans les techniques courantes de synthèse et de caractérisation des polymères sont souhaitables. Par exemple : caractérisation RMN et SEC, analyse thermique par DSC ; caractérisation morphologique (MEB) ; essais mécaniques. Une expérience dans le domaine de l'impression 3D de matériaux polymères et de la mise en forme des thermoplastiques serait un plus.
Pour toute thèse proposée au sein de l'Ecole Doctorale, le futur doctorant devra bien être titulaire d'un master (diplôme de master ou d'ingénieur français ou étranger, …) avec au moins une mention AB.
Dans tous les cas (diplôme de master ou d'ingénieur français ou étranger, …) le dossier doit comporter :
• le CV du candidat et lettre de motivation
• les notes obtenues au diplôme conférant le grade de master, mention 'Assez Bien' requise au minimum et copie du diplôme s'il est disponible
• 2 lettres de recommandations émanant du Responsable de la filière de formation et du tuteur de stage de fin d'études
• des éléments tangibles sur l'initiation à la recherche (mémoire de recherche, publication, ...).
Le dossier complet de candidature doit être envoyé à la direction de thèse par l' adresse messagerie : cecile.nouvel@univ-lorraine.fr
Candidate profile
The candidate should have an engineering degree or a Master 2 research degree, in materials science, chemical engineering, polymer processing or polymer Chemistry. Skills in current synthesis and characterization of polymers are desirable. For example: NMR et SEC characterization, analysis by DSC; morphological characterization (SEM); mechanical testing. Experience in 3D Printing of polymer materials and thermoplastic processing would be appreciated.
All applicants to the Doctoral School SIMPPÉ must have successfully completed a Master degree or its equivalent with a grade comparable to or better than the French grade AB (corresponding roughly to the upper half of a graduating class). In all cases (French or foreign Master degree, engineering degree, etc.) the counsel of the doctoral school will examine the candidate's dossier, which must include:
• CV and letter of motivation
• the grades obtained for the Master (or equivalent) degree and a copy of the diploma if it is available
• 2 letters of recommendation, preferably from the director of the Master program and the supervisor of the candidate's research project
• written material (publications, Master thesis or report, etc.) related to the candidate's research project.
The complete application file must be sent by email : cecile.nouvel@univ-lorraine.fr
Référence biblio
[1] N. Guo and M. C. Leu. Additive manufacturing: technology, applications and research needs, Front. Mech. Eng., 8 (2013), 215–243
[2] S. Ligon, R. Liska, J. Stampfl, M. Gurr, and R. Mülhaupt, Polymers for 3D Printing and Customized Additive Manufacturing, Chem. Rev., 117 (2017), 10212−10290
[3] F. Cruz, H. Boudaoud, S. Hoppe, M. Camargo, Polymer Recycling in an Open-Source Additive Manufacturing Context: Mechanical Issues. Additive Manufacturing, 17 (2017), 87-105,
[4] C. Suescun Gonzalez, F A. Cruz Sanchez, H Boudaoud, C. Nouvel, J M. Pearce, Multi-material distributed recycling via material extrusion: recycled high density polyethylene and poly (ethylene terephthalate) mixture, Polymer Engineering and Science 2024 https://doi.org/10.1002/pen.26643
[5] E. Lopes, L. R., Silva, A. F., & Carneiro, O. S. (2018). Multi-material 3D printing: The relevance of materials affinity on the boundary interface performance. Additive Manufacturing, 23 (2018), 45–52.
[6] Li Z.H.; Hu G.H; Corriou J.P.; Hoppe S.; Fonteix, C.; Laine, R.; Habimana, J.; Deheunynck D. A reactive extrusion process for the free radical grafting of silanes onto polypropylene: Effects of processing conditions and properties of water cross-linked silane-grafted polypropylene Polymer Engineering and Science, 53, (2013), 1571-1581,
[6] L. M. Forero Ramirez, A. Boudier, C. Gaucher, J. Babin, A. Durand, J.-L. Six, C. Nouvel Dextran-covered pH-sensitive oily core nanocapsules produced by interfacial Reversible Addition-Fragmentation chain transfer miniemulsion polymerization Journal of Colloid and Interface Science., 569(2020), 57-67 DOI https://doi.org/10.1016/j.jcis.2020.02.066
[7] C. Boyer, M. R. Whittaker, C. Nouvel, T. P. Davis,Synthesis of Hollow Polymer Nanocapsules Exploiting Gold Nanoparticles as Sacrificial Templates. Macromolecules, 43 (2010), 1792-1799.
[8] K. Estelle, D. Blair, K. Evans, B. Arda Gozen Manufacturing of smart composites with hyperelastic property gradients and shape memory using fused deposition, Journal of Manufacturing Processes, 28 (2017), 500-507